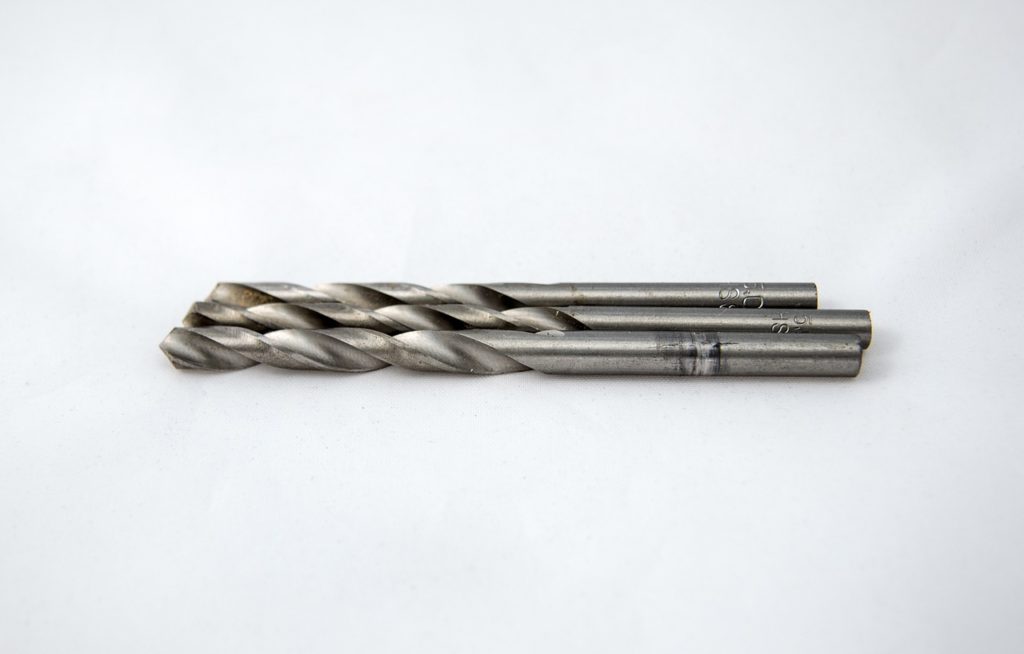
Wprowadzenie do pojęcia obróbki metalu i jej znaczenia w przemyśle
Obróbka metalu to proces przetwarzania surowca w wyroby gotowe, które znajdują zastosowanie w różnych gałęziach przemysłu. Polega ona na zmianie kształtu, wymiarów i właściwości mechanicznych materiału poprzez cięcie, gięcie, toczenie czy frezowanie. Obróbka ta jest niezbędna do produkcji elementów maszynowych oraz narzędzi potrzebnych do pracy innych urządzeń.
Współczesny przemysł opiera się na obróbce metali – bez niej trudno sobie wyobrazić funkcjonowanie wielu dziedzin gospodarki. Metalowe konstrukcje są podstawą budowy mostów, dróg czy linii kolejowych. Urządzenia elektroniczne i mechaniczne również zawierają wiele elementów wykonanych z metalu lub pokrytych warstwą tego surowca dla zapewnienia im odpowiedniej odporności i trwałości.
Znaczenie obróbki metalu wynika także z faktu, że pozwala ona na uzyskanie produktów o wysokiej precyzji wykonania oraz doskonałych właściwościach użytkowych. Dlatego też branża motoryzacyjna korzysta ze specjalistycznej obróbki metali przy produkcji silników samochodowych czy układów hamulcowych. Wielkie korporacje produkcyjne inwestują w nowoczesną technologię pozwalającą na jeszcze bardziej zaawansowaną obróbkę metali, co przekłada się na jakość i wydajność produkowanych przez nie produktów.
Obróbka metalu to proces wymagający specjalistycznej wiedzy oraz odpowiedniego sprzętu. Wymaga ona także stosowania różnych technologii, które pozwalają na uzyskanie pożądanych właściwości materiału. Dlatego też coraz więcej firm oferuje usługi z zakresu obróbki metali dla innych przedsiębiorstw, co pozwala im skupić się na swojej podstawowej działalności i osiągnięciu sukcesu na rynku.
Omówienie technik obróbki metalu, takich jak skrawanie, wiercenie, frezowanie i toczenie
Techniki obróbki metalu to procesy, które pozwalają na przetwarzanie surowych materiałów w gotowe produkty. Jednym z najpopularniejszych sposobów jest skrawanie, czyli usuwanie nadmiaru materiału za pomocą narzędzi tnących. Skrawanie może być wykonywane ręcznie lub przy użyciu maszyn CNC i pozwala na uzyskanie precyzyjnych kształtów oraz gładkiej powierzchni.
Inną popularną techniką obróbki metalu jest wiercenie, czyli tworzenie otworów o różnej średnicy i głębokości. Wiertła mogą być wykonane z różnych materiałów, takich jak stal szybkotnąca lub węglik spiekany, co wpływa na ich trwałość i jakość pracy. Wiercenie może być wykonywane zarówno ręcznie, jak i za pomocą specjalistycznych maszyn.
Frezowanie to kolejna metoda obróbki metalu polegająca na usuwaniu nadmiaru materiału poprzez ruch obrotowy frezu. Frezy są narzędziami tnącymi o różnej geometrii i przeznaczeniu – mogą służyć do tworzenia rowków, wgłębień czy też precyzyjnego kształtowania detali. Frezowanie wymaga dużej precyzji oraz odpowiedniego doboru parametrów pracy dla danego materiału.
Ostatnią omawianą techniką obróbki metalu jest toczenie, czyli przecinanie materiału za pomocą narzędzia tnącego poruszającego się wzdłuż osi obrotowej. Toczenie pozwala na uzyskanie precyzyjnych kształtów i gładkich powierzchni, a także umożliwia wykonywanie różnego rodzaju gwintów i otworów. W zależności od potrzeb, można stosować różne rodzaje tokarek oraz narzędzi tnących.
Wszystkie wymienione techniki obróbki metalu mają swoje specyficzne zastosowania i wymagają odpowiedniego przygotowania oraz doboru narzędzi. Dlatego też warto skorzystać z usług specjalistycznych firm zajmujących się obróbką metali, które posiadają nie tylko odpowiedni sprzęt, ale również wiedzę i doświadczenie w tej dziedzinie.
Zastosowanie temperatury do obróbki metalu, w tym hartowanie, odpuszczanie i przegrzewanie
Temperatura jest jednym z kluczowych czynników wpływających na właściwości mechaniczne metali. Zastosowanie odpowiedniej temperatury pozwala na uzyskanie pożądanych cech, takich jak twardość czy odporność na zużycie. Jedną z najważniejszych metod obróbki cieplnej metalu jest hartowanie.
Hartowanie polega na nagrzaniu metalu do wysokiej temperatury, a następnie szybkim schłodzeniu go w specjalnych płynach chłodzących. Dzięki temu procesowi uzyskuje się bardzo dużą twardość i wytrzymałość materiału, co sprawia że staje się on bardziej odporny na uszkodzenia mechaniczne.
Odpuszczanie to kolejna metoda obróbki cieplnej stosowana przy produkcji elementów ze stali oraz innych metali. Polega ona na ogrzewaniu hartowanego już wcześniej materiału do określonej temperatury przez pewien czas, a następnie stopniowym jego ochładzaniu. Proces ten zmniejsza twardość materiału oraz poprawia jego plastyczność i giętkość.
Należy jednak pamiętać o tym, że przegrzewanie może prowadzić do niekorzystnych skutków dla struktury metalu. Przy zbyt wysokiej temperaturze może dochodzić do rozpuszczenia poszczególnych faz lub też powstawania nowych faz o niepożądanych właściwościach. Dlatego też ważne jest, aby procesy obróbki cieplnej były dokładnie kontrolowane i przeprowadzane w odpowiednich warunkach.
Podsumowując, zastosowanie temperatury do obróbki metalu pozwala na uzyskanie pożądanych cech mechanicznych materiału. Metody takie jak hartowanie czy odpuszczanie są niezbędne przy produkcji elementów o wysokiej wytrzymałości oraz twardości. Jednakże należy pamiętać o tym, że procesy te wymagają precyzji i kontroli ze strony specjalistów zajmujących się obróbką cieplną metali.
Techniki poprawiania i modyfikowania powierzchni metalu, takie jak malowanie, galwanizacja
Techniki poprawiania i modyfikowania powierzchni metalu, takie jak malowanie czy galwanizacja, są niezwykle ważne w przemyśle. Metal jest materiałem bardzo trwałym i odpornym na wiele czynników zewnętrznych, jednakże jego powierzchnia może ulec uszkodzeniu lub korozji. Dlatego też stosuje się różnego rodzaju techniki mające na celu ochronę oraz estetyczną poprawę wyglądu metalowych elementów.
Jednym z najpopularniejszych sposobów na poprawienie wyglądu powierzchni metalowej jest malowanie. Malowanie pozwala na pokrycie metalu farbą lub lakierem, co chroni go przed korozją oraz nadaje mu nowy kolor i wygląd. Istnieje wiele rodzajów farb dostępnych na rynku przeznaczonych do malowania metali – od tych szybkoschnących po te bardziej trwałe i odporne na działanie promieni UV.
Inną popularną techniką modyfikacji powierzchni metalowej jest galwanizacja. Polega ona na pokryciu metalowego elementu cienką warstwą innego materiału za pomocą prądu elektrycznego. Najczęściej używanymi materiałami do galwanizacji są złoto, srebro czy chrom. Galwanizacja umożliwia uzyskanie efektownych wzorów oraz dodatkowo chroni przed korozją.
Niezależnie od wybranej techniki, ważne jest odpowiednie przygotowanie powierzchni metalowej przed przystąpieniem do modyfikacji. Powinna ona być dokładnie oczyszczona z brudu i rdzy, a także wypolerowana. W ten sposób uzyska się lepszą przyczepność farby lub galwanizatu oraz zapewni dłuższą trwałość efektu końcowego.
Różne metody spawania metalu, w tym spawanie łukowe, gazowe i laserowe
Spawanie metalu to proces łączenia dwóch lub więcej elementów metalowych w celu stworzenia jednej, spójnej całości. Istnieje wiele różnych metod spawania metalu, ale trzy z najpopularniejszych to: spawanie łukowe, gazowe i laserowe.
Spawanie łukowe polega na wykorzystaniu prądu elektrycznego do generowania ciepła i topienia materiału. W tym procesie elektroda jest podgrzewana do wysokiej temperatury przez łuk elektryczny między nią a materiałem bazowym. Spoina powstaje poprzez stopienie obu elementów i ich połączenie ze sobą. Ta metoda jest stosowana w wielu branżach przemysłowych, takich jak budownictwo czy produkcja samochodów.
Spawanie gazowe polega na wykorzystaniu płomienia gazu jako źródła ciepła do topienia materiału. Proces ten wymaga specjalistycznych urządzeń oraz mieszanki gazu o odpowiednim składzie chemicznym. Spoina powstaje poprzez stopienie elementów i ich połączenie ze sobą przy użyciu strumienia gorącego gazu. Metoda ta jest często stosowana w przemyśle rurarskim oraz naprawach maszyn rolniczych.
Spawanie laserowe to nowoczesna metoda łączenia metalu za pomocą wiązki światła lasera o dużej mocy. W tym procesie energia lasera jest skupiana na małym obszarze materiału, co powoduje jego topnienie i połączenie z innymi elementami. Ta metoda umożliwia precyzyjne łączenie nawet bardzo cienkich blach metalowych oraz minimalizuje ryzyko odkształceń czy uszkodzeń materiału.
Kształtowanie metalu przez tłoczenie, wyciskanie, gięcie i kucie
Kształtowanie metalu to proces, który umożliwia przekształcenie surowego materiału w gotowy produkt. Jednym z najpopularniejszych sposobów kształtowania jest tłoczenie. Polega ono na wprowadzeniu metalowej blachy do formy i wykorzystaniu siły hydraulicznej do jej uformowania. Tłoczenie stosuje się między innymi przy produkcji elementów samochodowych, sprzętu AGD czy artykułów gospodarstwa domowego.
Wyciskanie to kolejna metoda kształtowania metalu, która polega na przepuszczaniu go przez specjalne matryce o określonym kształcie. Dzięki temu możliwe jest uzyskanie różnorodnych detali takich jak pręty, rury czy profile aluminiowe. Wyciskanie jest szczególnie popularne w branży budowlanej oraz meblarskiej.
Gięcie to proces polegający na zmianie kierunku lub nachylenia powierzchni metalowej blachy bez naruszania jej struktury krystalicznej. Wykorzystuje się je przy produkcji elementów dekoracyjnych, a także w przemyśle motoryzacyjnym i lotniczym przy produkcji skomplikowanych części maszyn.
Ostatnią metodą kształtowania metalu jest kucie – technologia ta pozwala uzyskać bardzo trwałe i odporne mechanicznie produkty. Polega ona na uderzaniu metalu młotem lub prasą hydrauliczną w celu nadania mu pożądanych kształtów. Kucie stosuje się między innymi przy produkcji narzędzi, elementów maszyn oraz części samochodowych.
Wszystkie wymienione metody kształtowania metalu mają swoje zalety i wady, dlatego wybór odpowiedniej technologii zależy od indywidualnych potrzeb i wymagań danego projektu czy produktu. Bez względu na to, którą metodę wykorzystamy – tłoczenie, wyciskanie, gięcie czy kucie – ważne jest zachowanie odpowiednich standardów jakościowych oraz dbałość o bezpieczeństwo pracy podczas procesu produkcji.
Techniki cięcia metalu, takie jak tnące, skrawające i laserowe
Techniki cięcia metalu są niezbędne w wielu dziedzinach przemysłu, od produkcji samochodów po budowę maszyn. Istnieje wiele różnych sposobów cięcia metalu, ale trzy z najpopularniejszych to tnące, skrawające i laserowe.
Cięcie tnące jest jednym z najstarszych sposobów cięcia metalu. Polega na użyciu noża lub piły do przecięcia materiału. Ten proces może być stosowany do cięcia cienkich blach lub grubszych rur i profili stalowych.
Cięcie skrawające wykorzystuje ostrza podobne do tych używanych w gilotynie. Materiał jest umieszczany na stole roboczym, a następnie ostrze porusza się w dół i przecina go. Ta technika jest często stosowana do obróbki płyt stalowych o dużej grubości.
Cięcie laserowe to nowoczesna metoda cięcia metalu za pomocą wiązki lasera o wysokiej mocy. Laser precyzyjnie kieruje światło na powierzchni materiału, co powoduje jego stopniowe topienie i oddzielanie się od reszty płyty czy profilu. Ta metoda zapewnia bardzo dokładny wynik bez uszkadzania pozostałej części materiału.
Wszystkie te techniki mają swoje zalety i ograniczenia oraz wymagają specjalistycznej wiedzy i sprzętu. Wybór odpowiedniej metody cięcia zależy od rodzaju materiału, grubości i wymaganego wyniku końcowego.
W dzisiejszych czasach technologie cięcia metalu stale się rozwijają, a nowe metody pojawiają się na rynku. Jednak tnące, skrawające i laserowe pozostaną kluczowymi technikami w przemyśle metalowym przez długi czas.
Zastosowanie chemikaliów do obróbki metalu, takie jak elektrolityczne polerowanie, wybielanie i pasywacja
Zastosowanie chemikaliów do obróbki metalu jest niezbędne w wielu dziedzinach przemysłu. Elektrolityczne polerowanie, wybielanie i pasywacja to jedne z najpopularniejszych metod stosowanych w procesie obróbki metali.
Elektrolityczne polerowanie polega na umieszczeniu przedmiotu metalowego w roztworze elektrolitu, a następnie podłączeniu go do prądu stałego. Dzięki temu procesowi powierzchnia metalowa zostaje równomiernie oczyszczona i nabiera połysku. Metoda ta znajduje zastosowanie m.in. przy produkcji elementów dekoracyjnych oraz medycznych.
Wybielanie natomiast polega na usunięciu warstwy tlenków lub innych substancji organicznych z powierzchni metalowej za pomocą specjalnego preparatu chemicznego. Proces ten jest szczególnie popularny w branży jubilerskiej, gdzie stosuje się go przy produkcji biżuterii ze srebra czy złota.
Pasywacja natomiast ma na celu stworzenie na powierzchni metalowej cienkiej warstwy tlenkowej, która chroni ją przed korozją i utrudnia adhezję brudu oraz innych substancji chemicznych. Metoda ta jest często stosowana przy produkcji elementów maszynowych czy konstrukcyjnych wykonanych ze stali nierdzewnej.
Należy jednak pamiętać, że stosowanie chemikaliów do obróbki metalu wymaga odpowiedniej wiedzy i doświadczenia. Niewłaściwe użycie preparatów chemicznych może prowadzić do poważnych uszkodzeń przedmiotu lub nawet zagrożenia dla zdrowia człowieka.
Przedstawienie innowacyjnych metod obróbki metalu, takich jak obróbka elektroerozyjna, druk 3D i wytwarzanie za pomocą laserów
W dzisiejszych czasach innowacyjne metody obróbki metalu, takie jak obróbka elektroerozyjna, druk 3D i wytwarzanie za pomocą laserów stają się coraz bardziej popularne. Obróbka elektroerozyjna to proces usuwania materiału z metalu poprzez wykorzystanie prądu elektrycznego. Jest to bardzo precyzyjna metoda, która pozwala na uzyskanie dokładnych kształtów oraz doskonałych powierzchni.
Druk 3D to kolejna innowacyjna metoda obróbki metalu. Polega ona na tworzeniu trójwymiarowych obiektów z użyciem specjalistycznej drukarki 3D. Metoda ta umożliwia szybkie prototypowanie oraz produkcję małoseryjną elementów o skomplikowanych kształtach.
Kolejnym sposobem na obróbkę metalu jest wytwarzanie za pomocą laserów. Ta technologia polega na przeprowadzaniu strumienia światła laserowego przez materiał, co prowadzi do jego stopienia lub odparowania. W ten sposób można uzyskać bardzo precyzyjne cięcie lub spawanie elementów metalowych.
Innowacyjne metody obróbki metalu mają wiele zalet, takich jak wysoka precyzja wykonania czy możliwość produkcji skomplikowanych kształtów. Dodatkowo pozwalają one na oszczędność czasu i kosztów produkcji. Dzięki temu coraz więcej firm decyduje się na wykorzystanie tych nowoczesnych technologii w swojej działalności.
Należy jednak pamiętać, że każda z tych metod ma swoje ograniczenia i wymaga specjalistycznej wiedzy oraz sprzętu. W przypadku obróbki elektroerozyjnej konieczne jest posiadanie odpowiedniego generatora prądu elektrycznego, natomiast druk 3D wymaga stosowania specjalistycznych materiałów do druku. Warto więc dokładnie przeanalizować potrzeby przedsiębiorstwa i wybrać najlepszą metodę dla danej sytuacji.